What are CMMS software and their benefits?
- kiakahhali
- Feb 19, 2021
- 2 min read
Updated: Feb 20, 2021
CMMS stands for “Computerized Maintenance Management Systems”.
Implementing CMMS software delivers comprehensive maintenance management, putting organizations in control of their assets, reducing critical equipment downtime, and cutting overall maintenance costs.
Developments in technology during the past decade have transformed and shaped how we conduct our lives.
From banking to education and travel to health care, the non-stop evolution of technology has impacted almost every aspect of our daily lives.
In simple, technological advancements have made it possible to do things easier, quicker, and smarter.
One area in which computerization has emerged and shown itself to be exceptionally helpful is in the maintenance and equipment management area.
Until the past couple of decades, companies managed their assets using a pen and paper approach; hard copy work orders, schedules, asset folders, logbooks, lists, memos and possibly some excel sheets.
Managing, dispatching work orders and following up on the assigned tasks often took days, resulting in valuable time lost and production delays. Due to the dispersive nature of this approach, it was impossible to report timely and precisely.
Approaches like this one, are unresponsive burdens to the increasing demands for lean and efficient company operations.

More than ever, today’s operation, facility and asset managers are challenged to keep pace with changing industry trends and economic demands while at the same time being sensible of profit margins and returns on investments (ROI).
The current economic climate has resulted in an increasing number of companies turning toward CMMS systems as their main Equipment Management software.
CMMS platforms are best to be described as highly sophisticated software programs which utilize thousands of data points that can provide a user with an overview of a maintenance team operation or with the status and history of any given individual piece of equipment at any given time.
Current CMMS software offer businesses the ability to track work orders, quickly generate accurate reports and instantly determine which of their assets require preventive maintenance. CMMS also offers resource planning and real-time feedback on maintenance team workload, backlogs, and Performance KPI.
This improvement has led to extended equipment lifespans, improved organization, better time management as well as resource/labour utilization and ultimately, reduced operational costs and increased company profits.
Well-maintained equipment and assets are at the core of an efficiently managed operation. Poorly maintained equipment generally results in unexpected breakdowns, costly repairs, and often early and impulsive equipment replacement.
Conducting regular preventative maintenance using a preventive maintenance schedule is the best way to avoid unanticipated equipment failure while also extending their lifespan.
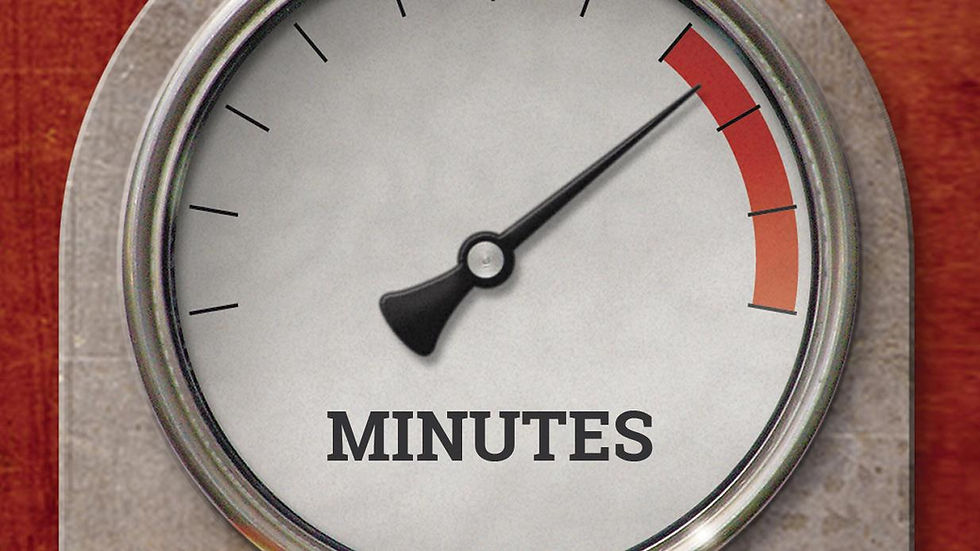
Reduce downtime by making the jump to preventive maintenance. Instead of waiting for assets to fail, proactively schedule inspections, and maintenance tasks to catch small issues before they develop into big problems.
When it comes to preventative maintenance, CMMS solutions create routine schedules, as well as provide efficient communication and organization tools to grab unanticipated events, send notifications and reminders, and generate reports.
The first step to controlling your budget is knowing where the money is going.
Robust tracking and real-time reports let you see the big picture of the maintenance program efficiency and the equipment park health profile which gain that oversight.
Author: Kia Kahhali
Comments